Industrial
H
oneywell’s AI Expert: Think about AI as an Augmenting Tool, Not an Artificial OneThe industrial sector has been slow to adopt artificial intelligence and machine learning, but having realised the error of its ways, the tech is now, in one form or another, being introduced to the factory floor. Daniel Davies speaks to Honeywell’s vice president and general manager of Connected Enterprises, Stephen Gold, about what the future holds for AI in the industrial sector
When Honeywell, the technology and manufacturing firm working in industries as diverse as aerospace, smart homes and oil and gas, announced that Stephen Gold would be joining the business as vice president and general manager of Connected Enterprises, it was a clear sign of the company’s immediate ambitions.
Gold had spent the previous seven years working for IBM, which had acquired his previous employers SPSS in 2009. For most of his time at IBM, Gold worked on the company’s – and perhaps the world’s – most famous artificial intelligence solution, Watson.
Upon his arrival at Honeywell in February 2017, Gold made it clear that figuring out how the company could use AI would be at the top of his to-do list. "Our focus will bring together the physical world with data and digital intelligence, including next-generation artificial intelligence (AI) technology and advanced analytics,” said Gold at the time.
Like IBM, Honeywell has fingers in many pies, and for a company that serves both commercial and consumer sectors, as well as a host of industries, the appeal of AI and leveraging data is obvious. Gold, for example, talks of being able to employ “predictive maintenance” in industry, where a pump, a valve or an actuator in a factory could be adjusted so that it always works in an optimised state.
But how far does Honeywell’s AI authority feel we are from that point, from realising AI’s potential? “This is not a mature market by any stretch of the imagination,” says Gold. “We hear a lot about machine learning and deep learning, and when we look at this we realise we're still 2 to 5 years out in terms of that technology starting to plateau.
“How about autonomous driving? It's here right? Well the reality is we're still decades away from having fully available autonomous cars, so we're at Level 2 today and we need to get to Level 5. The point being is that we're right on the early cusp of change. We collectively have an opportunity to influence how organisations will adapt and leverage this new technology.”
AI in industry
As Gold points out, consumer-related industries – retail, health and financial services – have already shown an appetite for AI, but the industrial sector has so far appeared reluctant to embrace the technology. While we’ve (even in the pages of this magazine) seen the occasional robot working alongside humans, the real value AI can provide industry is in allowing for the real-time analysis of data. Imagine the power a swarm of sensors littered around the factory floor could have if the data they contribute allows intelligent predictions to be made.
According to the International Data Corporation, there’s about 16 zettabytes of the data in the world today, but that number could climb to 163 zettabytes by 2025. This data will unlock new opportunities for all businesses, and it’s up to the industrial sector to take advantage.
“Largely the industrial sector has been performing and working well, so there's been relatively little change for an extended period, but it finds itself at a kind of inflection point where there's this interest to understand that physical-to-digital intersection,” says Gold. “Physical things obviously have a purpose and perform a task and that's interesting; it turns out it's much more interesting if you start to make them intelligent and instrument them and make them interconnect; it tells a very different story.
“The ability to connect, for example, a factory on the shop floor, and understand the dependencies of the machinery and the people and the process allows you to be much more effective and to keep things up and operational, to do predictive maintenance, to start to apply prescriptive analytics so that you don't have to have unforeseen circumstances compromise the integrity of the operation.”
“The industrial sector has been performing and working well, so there's been relatively little change for an extended period, but it finds itself at a kind of inflection point.”
Historically, the data that has been available to the industrial sector has been structured data or information neatly organised into rows and columns. But the type of data that's going to become overwhelming is unstructured data. Maintenance reports, user manuals, customer feedback, video: this is the data that will unlock new opportunities for industry.
“A typical oil refining plant costs upwards of $750m to build. That plant operation, if it ceases to occur on a single day, cost about $1m. A typical liquid natural gas plant will have five unplanned shutdowns per year costing upwards of $25m. Why? Well because the connected devices didn't connect or didn't transmit or didn't tell us what was likely to happen. What was likely to fail,” says Gold. “If I know that in advance I can take corrective action. I can better manage my assets. I can better affect my people.”
General intelligence versus specific intelligence
Even given the slow uptake, industrial companies have moved on, or are in the process of moving on, from simple recording and reporting and are now focused on collecting data to be able to make intelligent predictions. The next step, however, is to have sensors that learn the behaviour of a particular device and make adjustments without intervention, so that devices can repair and maintain themselves.
To get to the point where machines can maintain themselves though, you have to train the system, and to train the system you have to have enough data or ground truth.
“Ground truth is this idea that I have an input and an output and I have enough of those relationships that I actually can train the system. In most cases there's not sufficient ground truth to provide accurate training to get to a level of confidence to allow that level of systematic operation, and so we're just now starting to concentrate on that data collection,” says Gold.
“The other part of it too is it's not just the data you collect from the device, it's the data about the device, data about the surroundings, the facility, the environment, the characteristics of the factory and output, so there's a lot of data points that have to be collected, a lot of ground truth that has to be aggregated to start to train this, and it's going to take years.”
“You can ask me about food, about mathematics, about philosophy and I can instantly adapt. We're not anywhere close today to having the capability of doing artificial general intelligence.”
The end goal for the industrial sector is for its machines to be capable of adapting – to their environment, to challenges and to working with different people – but for that to happen they would need to develop general intelligence, or intelligence that is comparable to the human brain, but as Gold explains at this moment in time we’re not even close to imbuing AI with that kind of ability.
“Today what we're focused on is what they call artificial specific intelligence, and that really training something around one output, so think about training someone on mathematics, it's a single science. That's very different from artificial general intelligence," explains Gold.
"We as humans operate more around artificial general intelligence. You can ask us anything. You can ask me about food, about mathematics, about philosophy and I can instantly adapt. We're not anywhere close today to having the capability of doing artificial general intelligence, so a device can certainly benefit from specific intelligence, and that's what we're trying to do, but ultimately we want it to evolve to general intelligence to adapt to all things that matter at that moment in time, and that's decades, I mean literally decades away,” says Gold.
“We'll see this kind of natural evolution of statistical modelling, neural networks, it'll be followed by more applications and machine learning of this probabilistic science, it'll then move naturally into more deep learning, unsupervised learning all the way out to artificial general intelligence.”
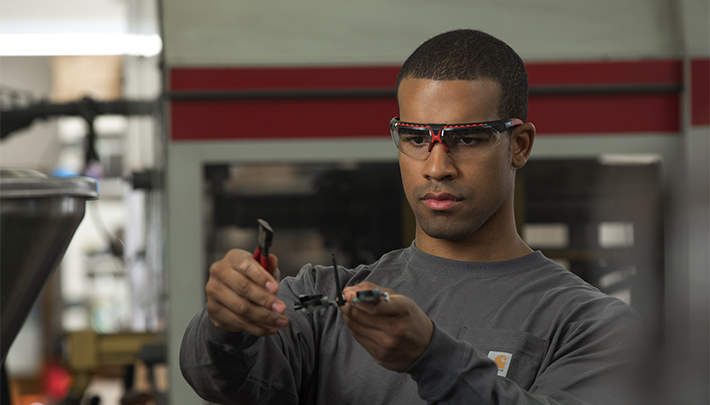
AI: augmenting intelligence
For industry to really benefit from AI, though, it’s not just about adding sensors to the environment; it’s about ‘sensorising’ workers and then extending their physical capabilities. Gold himself doesn’t solely think of AI as a quest to artificially engineer intelligence, but rather as a tool to augment intelligence. He argues that by thinking about AI in this way, it becomes very familiar and comfortable to us, rather than something to be feared.
“The average individual can bench press about 60kg, impressive to itself. They can deadlift about 70kg, but that same individual in 1896 created the first steam shovel and that steam shovel could lift a little over 7,300kg, so man overcame its physical limitation by inventing something that could lift an extraordinary amount of weight,” says Gold.
“The human eye is only second in complexity to the human brain, the human eye has about 2 million moving parts, we're capable of discerning about 256 shades of grey, about 2.5 million colours and on a clear day we can see out about 5km, but again man overcame that physical limitation in the creation of the Hubble telescope, capable of seeing out about 15 billion light years. Artificial augmentation isn't unusual; we're actually pretty familiar with it.”
“Artificial augmentation isn't unusual; we're actually pretty familiar with it.”
Gold and Honeywell are beginning to make this idea of augmenting humans, and specifically industrial workers, come to pass by equipping them with simple sensors that monitor their surroundings, so things like air temperature, air quality and geo-location tracking. These sensors not only give businesses information about the workplace, they also allow companies to monitor the health and safety of their employees.
“We would know how long a worker spent in a particular area, potentially an area that is compromised or has exposure limits, so I think that it's a combination of outfitting the worker with better equipment, starting with sensors, and then extending the job that they do with instrumentation, be it hand-held devices and such,” says Gold.
“A lot of this is becoming much more affordable through the use of basic accepted operating environments like Android or IOS, through some very traditional devices like mobile devices that are ruggedised for the shop floor. I think at one time some of these instrumentation and outfitting of a worker were cost prohibitive, but they now come in line.“
Obviously, there's a balance to be had and there needs to be a purpose to collecting data on workers, but Gold says that in the industries Honeywell operates in, he has so far heard no complaints.
“The idea of outfitting the worker has been well received to ensure that that worker goes home safe at night,” says Gold. “It provides a peace of mind that is second to none, so hard hats fitted with accelerometers to know if there's been a situation or incident rather than finding the worker compromised hours later are invaluable.”
Images courtesy of Honeywell