Manufacturing
Tempo Automation: Inside the PCB Smart Factory Where Robots Program Themselves
Printed circuit boards are an essential part of modern life, with demand in almost every sector. Berenice Baker hears from Brady O Bruce, CMO of Tempo Automation, about how the company’s smart factory is revolutionising their delivery
Tempo Automation has built a 42,000 square-foot industrial internet of things (IIOT) smart factory in San Francisco’s downtown Design District to deliver printed circuit board (PCB) assembly prototypes for top innovators in aerospace, medical technology and industrial electronics. Its PCBs will even soon be found on the surface on Mars.
“PCBs are in every piece of electronics you have sitting in front of you – your laptop, phone and of course anything from aircraft, satellites, submarines, vehicles, medical devices and even the machinery you might find in a modern factory,” explains Brady O Bruce, CMO of Tempo.
While high-volume PCBs are typically made in Asia and other parts of the world, Tempo’s mission is to get hardware makers through the prototyping phase as quickly as possible by focusing on the low-volume, high-mix end.
“Factories in our segment of the business have to be able to produce different kinds of PCBs many times a day and adjust between the different orders that a customer provides. Our factory has to change and be set up to produce a variety of boards for different applications; the trick is to do that as quickly as possible and the highest quality possible.”
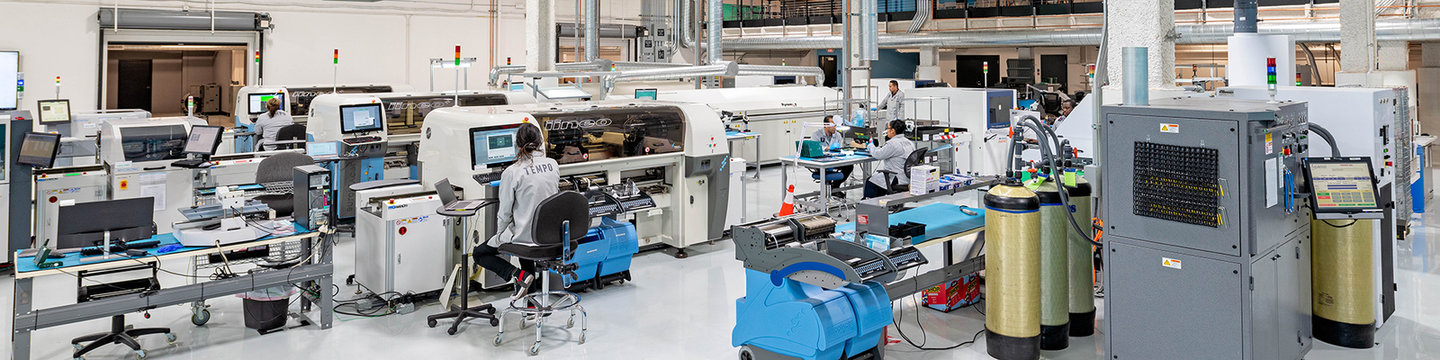
Using robotics in smart manufacturing
Bruce admits that the factory does not use AI in its strictest sense. Tempo’s proprietary factory automation software has revolutionised smart manufacturing using IIoT and learning robots. Typically in prototype PCB manufacturing, customers transmit plans via FTP or email then a team of designers take a look at that design and assemble by hand a bill of materials and give the customer a quote on delivery and cost.
“Our approach is a little different,” says Bruce. “The customers submit their designs and our software examines it and does several things at once far more quickly than people can. It looks at the design and begins what is called feature extraction; it imagines what it will look like when it’s finally designed and provides a photo-realistic image of that PCB for the customer. It’s indistinguishable from photos of the finished board.”
This helps the software understand the design, and if there are any issues with the design and replacing a component might cure the problem, it will communicate them back to the system. At the same time, the software seeks out the necessary components and makes judgements about which suppliers would be most likely to get them to Tempo on time. This means customers can get a quote within a couple of hours rather than a matter of days.
“Our software actually programs all the machines in that production line in a matter of minutes, and it’s ready on the day or hour the customer approved the order.”
Once Tempo has the go-ahead, production can begin. It uses off-the-shelf machines and reprograms them to work better and communicate with each other.
The first machine on a PCB production line is a solder mask, which puts down the solder on the board to which the components will be affixed, then the pick and place machine, a robot that puts the components on the board, then the reflow oven which heats the board up in such a way that the solder becomes solid and the parts and properly fixed. Traditionally, each would take hours to process separately.
“Instead of that, our software actually programs all the machines in that production line in a matter of minutes, and it’s ready on the day or hour the customer approved the order,” says Bruce.
“When all the parts are ready, they’re scanned in, and the software announces that it’s ready to begin the build. And all of that combined work done in a very short period of time has already saved many days off a typical process.”
Design for manufacture: a “deep look” at design
Taking place parallel to the work on quoting and seeking parts is the design for manufacture (DFM) study.
“DFM is a very deep look at the design and makes judgement about whether the board can be built and whether it can be built with the machines we have in the factory,” explains Bruce. “The DFM study alone typically takes a week for most manufacturers; our system is able to perform a DFM study in three or four hours.”
All these processes are transparent to Tempo’s customers, who can track their orders via a dashboard tracker which reports progress live, earning it the nickname “pizza tracker”.
As the PCBs come off the production line, they are subjected to a battery of tests which are, of course, automated.
“The first test is called an automated optical inspection, or AOI, and our machine does something remarkable which a lot of AOI machines cannot do.”
“The first test is called an automated optical inspection, or AOI, and our machine does something remarkable which a lot of AOI machines cannot do,” claims Bruce.
“At the beginning of the process we create what we call a fabrication simulation; it is the ideal model of the product accompanied by a photorealistic image the customer can look at. The AOI machine is a very powerful camera that moves around very quickly on an XYZ gantry and is takes pictures of different parts of the board.
“In a manually-operated system, someone is looking around the board with a mouse on a screen. In this case, we program the AOI machine to look at specific places on the board and compare what it sees with that fabrication simulation. It knows what that board should look like and looks at specific places on the board – many hundreds of them – and compares what it’s seeing with what it’s supposed to look like and looking for the differences.”
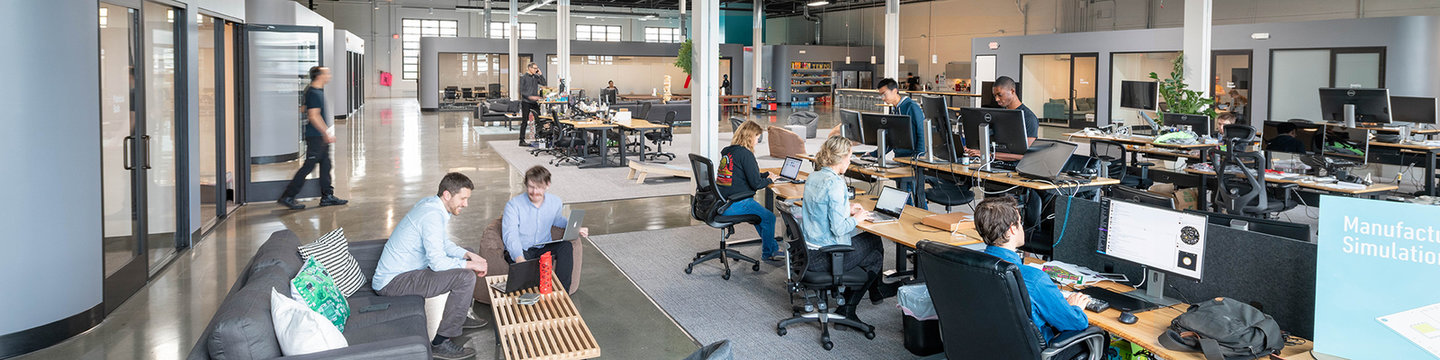
Quality control
The last step is to put boards through an X-ray machine to check the integrity of the components and carry out spot checks on solder and critical elements, again guided by Tempo’s software.
Tempo achieves this with off-the-shelf machines by asking the manufacturers for access to the low-level APIs to reprogram them.
“That’s also the interface by which we have the machines report what they’re doing into our own network that we call Tempocom,” says Bruce. “Tempocom is the hub for all this activity and the backbone around which all the structures in the factory and the customer interactions are built. It also reports that everything is working correctly and any problems that need attention.”
Tempocom has also replaced the ‘traveller’, a feature of traditional factories that even today often takes the form of a plain, manila file folder that accompanies the product through manufacture for an operator to tick off a stage before it progresses to the next machine.
“We call it the digital traveller,” says Bruce. “It lives within Tempocom and is transmitted to everyone on the factory floor through a mobile device like a phone. They can keep track of the process and be alerted when something needs attention.”
Holistic automation: Into space
This holistic approach to automation has delivered demonstrable benefits to Tempo’s customers, including Lockheed Martin, for whom Tempo reduced the target delivery time for a PCB to detect flutter on aircraft from 22 months to 11.
“For Lockheed Martin, being able to reduce the cycle time on a new product is immense,” says Bruce. “They’re building aircraft that cost millions of dollars and getting them on the market on time to meet a contract is essential. Oftentimes the one thing the process that’s most at risk is that prototyping phase. Lockheed liked what we do so much they also become an investor in our most recent series C funding round, which raised $45m in April.”
Tempo’s PCBs will even play a part in NASA’s Mars 2020 mission, which is set to launch next year and deposit the next generation of Martian rover on the surface.
“We built the prototype boards that are going into that mission, as well as some of the production boards that actually go to Mars,” says Bruce. “They’re associated with the live onboard audio-visual system which for the first time is going to allow people to see the landing on Mars as it takes place.”